11:30 - 13:00 Component reliability and diagnostics: early detection and intervention is key!
O&M & logistics


Room: Hall G1
This session will give an insight into wind turbine reliability and the state of the art in wind turbine diagnostics. It will look at how to collect and analyse reliability data in order to improve design as well as O&M strategies. This session will also look at the use of supervisory control and data acquisition (SCADA) data for condition monitoring: both 'conventional' ten minute data and higher frequency 1Hz data. Finally, there will be a case study of how power data from the converter can be used to infer wind turbine loading.
You attended this session?
Co-chair(s):
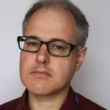

Presenter
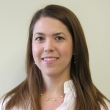
Co-authors:
Elizabeth Traiger (1) F
(1) DNV GL, Bristol, United Kingdom
Presenter's biography
Biographies are supplied directly by presenters at WindEurope Summit 2016 and are published here uneditedDr Traiger has been working in the wind industry for 7 years. She currently is a senior researcher at DNV GL based in Bristol, United Kingdom. Elizabeth studied mathematics at the University of Kansas and earned her doctorate in statistics at the University of Oxford. She has worked on wind project development, operational assessments, due diligence and grid integration projects throughout her career with companies in North and South America. Dr Traiger’s current research concerns advanced statistics and predictive analytics on large data sets.
Abstract
Give it all you got: using big data machine learning ensembles for condition monitoring
Introduction
Current engineering models approximate the real world. Up to now complexity in system interactions make exact real time system modelling outside the realm of possibility. Recent advances in computing in the ‘Big Data’ space have opened the door to the practical use of computationally intensive machine learning statistical techniques. These data-driven pattern recognition algorithms are well-suited to turbine gear box fault detection given the intricacy and abundance of existing high frequency SCADA data. Traditional failure models were limited to the use of 10-minute SCADA data and mainly temperature based signals. This work utilizes all 1 Hz signals coupled with expert knowledge to create an ensemble model to predict gear box failure faults.
Approach
Within a 'Big Data' computing architecture, high frequency SCADA sensor signals are are analysed using an ensemble machine learning algorithm. Quality controlled 1 Hz SCADA signals from multiple operational wind power projects installed with the same turbine technology are used as inputs to a supervised learning ensemble algorithm. Advanced statistical techniques including the use of gradient boosting machines and bagging, coupled with expert wind engineering knowledge in feature creation and feature selection, a data-driven model for gear box faults is created.
Main body of abstract
Support vector machines and ensemble gradient boosting machines were tested to identity gear box failures. Feature inputs to both models were chosen from all available 1 Hz SCADA signals. Testing on training data sets reduced the input size and optimized for computational speed. Feature dimension reduction was aided by consultation with expert condition monitoring engineers. A validation set was used to judge performance based on false positive rate and mean squared error. The gradient boosting machine outperformed the support vector machine model on both accuracy and speed metrics.
Conclusion
The work presented here shows how the use of large volumes of high-frequency SCADA data combined with powerful ensemble machine learning statistical algorithms provides improved condition monitoring algorithms for gear box fault prevention. Traditional techniques based purely on physical models and time averaged 10-minute SCADA data fail to capture the complex interactions between components. The use of 'Big Data' parallel computing architecture allows for enhanced real time conditions monitoring.
Learning objectives
The work presented here opens the door to the use of data driven Big Data parallel computing techniques to the Wind Industry. The statistical machine learning techniques of gradient boosting machines and bagging for ensemble algorithm creation will be explained. We illustrate how to combine data-driven pattern recognition techniques along with wind industry expert knowledge in superior preforming predictive model creation.
Follow EWEA on: