11:30 - 13:00 Component reliability and diagnostics: early detection and intervention is key!
O&M & logistics


Room: Hall G1
This session will give an insight into wind turbine reliability and the state of the art in wind turbine diagnostics. It will look at how to collect and analyse reliability data in order to improve design as well as O&M strategies. This session will also look at the use of supervisory control and data acquisition (SCADA) data for condition monitoring: both 'conventional' ten minute data and higher frequency 1Hz data. Finally, there will be a case study of how power data from the converter can be used to infer wind turbine loading.
You attended this session?
Co-chair(s):
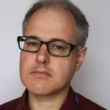

Presenter
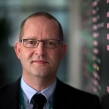
Co-authors:
Henrik Pedersen (1) F
(1) Siemens , Brande, Denmark
Presenter's biography
Biographies are supplied directly by presenters at WindEurope Summit 2016 and are published here uneditedHenrik has a background from electronics engineering, design and service. Now responsible for designing remote diagnostic systems for Siemens Wind Service. Currently he is heading the Model Based Diagnostic group within Diagnostic intelligence, at the diagnostic center in Brande, Denmark
Abstract
Reduce production loss through early-stage detection of abnormal behaviour
Introduction
A modern wind turbine is a complex and expensive machine.
Profitability is crucial for the investment and achieving this depends on a turbine’s performance and availability.
Approach
Data generated by turbines is used to model and compare new data.
Main body of abstract
A vast amount of data collected the recent emergence of exciting new data analytic capabilities,
and a massive knowledge base generated from developing and servicing wind turbines.
This is three facts that allows us to develop completely new types of tools and systems.
Model Based Diagnostics (MBD) is one of these tools
Serious issues can stop the turbines and require repair, mobilization of a service team, spare parts,
cause production loss and trigger travel costs that are particularly expensive when it comes to
offshore turbines.
The highly advanced and intelligent models can pre-calculate an expected value based on
learning algorithms like neural networks, local outlier factor, linear regression and so on,
and afterwards compare to the actual measured value. Any significant deviations will alert our experts,
and a detailed technical advice and troubleshooting guide can then be created to assist the customer,
or service technicians on site, to efficiently remedy the issue. This is done by automatically
raising a ticket in the internal case management system. The ticket is forwarded to the responsible
service planner, allowing the planner to assign a technician according to the predefined priority.
Conclusion
Model Based Diagnostics serves to detect the type of abnormal operational behavior, that if not addressed
in due time, may become a more serious issue.
Service planners can thereby be notified in advance of many issues, and prioritize and bundle remediation.
Learning objectives
Attendees will learn how Siemens effectively have leveraged the value of Wind Turbine sensor data,
and especially what to avoid, and where not to go, when deciding on a journey into carving information,
and value out of this vast amount of information
Follow EWEA on: