14:30 - 16:00 Advanced control strategies for wind plants
Turbine technology


Room: Hall G2
Modern control design methods like non-linear model predictive control can take account of complex dynamics and actuator constraints, while making use of richer information input from advanced sensors such as LIDARs. They contribute to the coordinated control of entire wind farms while meeting new operational demands from the electricity system. The session addresses advanced state estimation methods, an important component of such controllers. You will hear about field test results from a controller using wind preview from a LIDAR sensor as well as changes in design and certification guidelines needed to account for the use of LIDARs.
You attended this session?
Learning objectives
- Advanced non-linear state estimation techniques for wind turbines that run in real time;
- Non-linear model predictive control that rung in real time and improve performances;
- A LIDAR-assisted flatness-based controller validated in field tests;
- Requirements for design and certification of wind turbines with LIDAR assisted control;
- A wind farm control framework that can mitigate wake effects and provide grid balancing services.
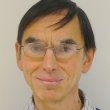
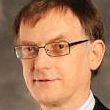
Presenter
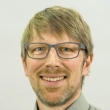
Co-authors:
Nikolai Hille (1) F Kai Freudenreich (1) Ervin Bossanyi (2)
(1) DNVGL - Energy, Renewables Certification, Hamburg, Germany (2) DNVGL - Energy, Research and Innovation, Bristol, United Kingdom
Presenter's biography
Biographies are supplied directly by presenters at WindEurope Summit 2016 and are published here uneditedAfter studying mechanical engineering at the University of Braunschweig, Germany, Mr. Hille has been working for 14 years at DNV GL Renewables Certification. Within his role as senior expert on wind turbine onshore loads he has been involved in numerous type and site-specific certification projects, developments of load standards for certification as well a research projects.
Abstract
Guidance for design and certification of wind turbines with LIDAR-assisted control
Introduction
The use of LiDAR assisted control for wind turbines is currently limited to research and development as well as prototype implementations but an increasing interest in the application of LiDAR assisted control in commercial wind turbine types and projects can be observed. At the same time standards for wind turbine design, which are available today, do not explicitly take into account special requirements associated with LiDAR assisted control of wind turbine. Aim of the work presented here is to identify the special requirements and to provide guidance on how to account for these special requirements.
Approach
Existing and proposed ways of integrating LiDAR assisted control strategies in wind turbine control systems has been analysed. Based on known characteristics of LiDAR systems, the capabilities, limitations and possible sources of errors were identified and it was analysed, if and how these characteristics are accounted for in existing standards and which gaps exist. Suggestions have then been developed on how to fill existing gaps in standards.
Main body of abstract
The LiDAR system has the task to remotely measure wind speed in front of the wind turbine. In spite of required calibration of the LiDAR system, availability, volumetric averaging and measurement error influence the data quality. To be useful for turbine control, LiDAR systems must evaluate if the measurements meet the defined accuracy and report an error, if this is not the case.
The LiDAR assisted control system uses the measured data from the LiDAR system for feed-forward control of the wind turbine as an extension to regular feed-back control techniques. Sanity checks on the performance of the LiDAR assisted control system shall be implemented in order to detect performance outside the expected range. The sanity checks shall support a differentiation between normal operation, a fault in the LiDAR system and a meteorological event not detected by the LiDAR system.
For a LiDAR assisted control system, several operational states need to be considered. A systematic approach for identifying relevant operational states such as an FMEA shall be followed and the availability of the LiDAR system shall be taken into account.
Within the aeroelastic simulation, the LiDAR system, a suitable turbulence evolution model and the LiDAR assisted control system shall be modelled in such way that the dynamic load behaviour of the wind turbine is reflected in the simulations. Load validation against measurements shall be performed to confirm the validity of assumptions made during the design phase.
As a minimum the design load cases according to the applicable load standards shall be considered for load analysis. These design load cases shall be supplemented by design load cases representing the specific features of LiDAR assisted control. If operation is possible with active and de-activated LiDAR system, both situations shall be included in the load analysis.
Conclusion
Guidance on how to apply existing standards for the design of wind turbines in conjunction with LiDAR assisted control has been developed. This way uncertainty regarding the application of LiDAR based control of wind turbines could be reduced.
Learning objectives
Requirements associated with the implementation of LiDAR assisted control of wind turbines are presented in this work.
Follow EWEA on: